
Mechanochemical synthesis and refinement of photovoltaic inks
The mechanochemical synthesis is a solid-state reaction activated by the transfer of mechanical energy and heat due to the impact, rolling and rubbing of grinding balls of suitable size and hardness against a mixture of precursor powders. This synthesis method exploits the non-equilibrium thermodynamics with raising local temperatures (up to 10000 K) at the moment of impact to induce solid-state chemical reactions, which are impossible to obtain by conventional synthesis techniques. The great advantage of the mechanochemical synthesis lies in the possibility of working in environmental conditions of pressure and temperature without solvents nor toxic chemical components. The simplicity of the grinding mechanism guarantees a very low process cost (depending on the market value of the precursors used) and a very high reaction yield (usually above 90-95%). Being mediated by the local non-equilibrium thermodynamics, by this synthesis method metastable phases can be attained, and solid state reactions of components with incompatible physical characteristics (reactions between compounds with different melting temperatures and vapor pressures) can be activated. In the Green Energy field, the mechanochemical synthesis is applied to chalcogenides and nitrides for photovoltaic applications , in particular the wide-band gap materials: Cu(In,Ga)(S,Se) 2 , CuSb(Se,S) 2 and (In,Ga)N. Once the powders of the materials obtained by mechanochemical synthesis are pressed and sintered in the oven, the starting targets for the deposition of thin films can be obtained using Low- Temperature Pulsed Electron Deposition and RF-Sputtering techniques available at IMEM. Planetary grinding is also used, once the desired product is obtained, to stabilize a submicrometric suspension of paints / inks with variable granular size and concentration ready to be deposited using low-cost and wide- impact techniques, such as ink-jet printing, aerojet -printing, spin coating, dip coating or simply by painting with a brush on suitable surfaces. Paint solutions with biocompatible solvents, such as water or simple alcohols, are studied: ethanol, iso-propanol and butanol. In our laboratory, mechanochemical reactions and dust refining operations are carried out with a fleet of high energy planetary ball mills (Pulverisette 7 Classic Line and Pulverisette 7 Premium Line, distributed by Fritsch GmbH, Fig. 1). Depending on the desired solid state reaction, the materials and the grinding conditions are selected and optimized. We have medium- hard (Agate / quartz) and high-hardness (Zirconia) jars, equipped with balls from 1 mm up to 10 mm in diameter. The speed of rotation of the jars (up to 1100 rpm), the weight ratio between balls and precursors (ball-to-powder ratio, BPR) and the duration and number of grinding cycles can be varied in a wide range depending on of the purpose and product of the process. It is also possible to work in liquid or dry, wet or dry ball milling, even with controlled atmosphere up to 20 bar pressure (with Pulverisette 7 Premium Line).
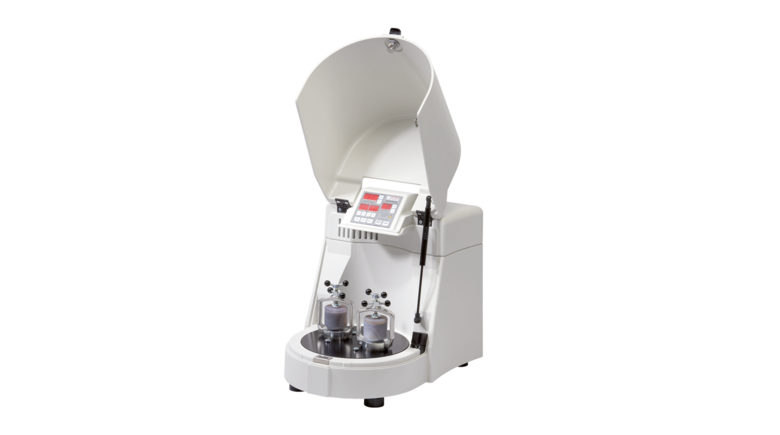
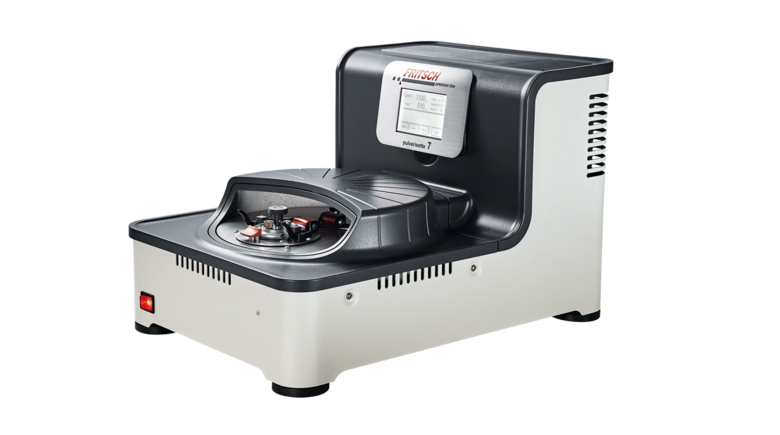
Planetary mills with high-energy balls: Pulverisette 7 Classic Line (left) and Pulverisette 7 PremiumLine (right), distributed by Fritsch GmbH.